Optionally, use 4 included screws to attach the board to the standoffs. Each corner of the TIEVM-MTR-HVINV has a circular hole for this purpose.
- If not already connected, connect the daughterboard to the top of the motherboard. The 2-row header of the motherboard (J15) should align with the 2-row connector of the daughterboard (J3).
- Key pin 8 of daughterboard connector J3 should be clipped if it is not already done.
- Observe the bottom of the XDS110ISO-EVM and locate the key pin. Connect the XDS110ISO-EVM to daughterboard connector J3, such that the key pins of each board are aligned.
- Verify the desired state of the daughterboard boot mode switch (S1).
- Connect motor wires to J10.
For the Estun EMJ-04APB22, the following is an example image showing how it may be connected:
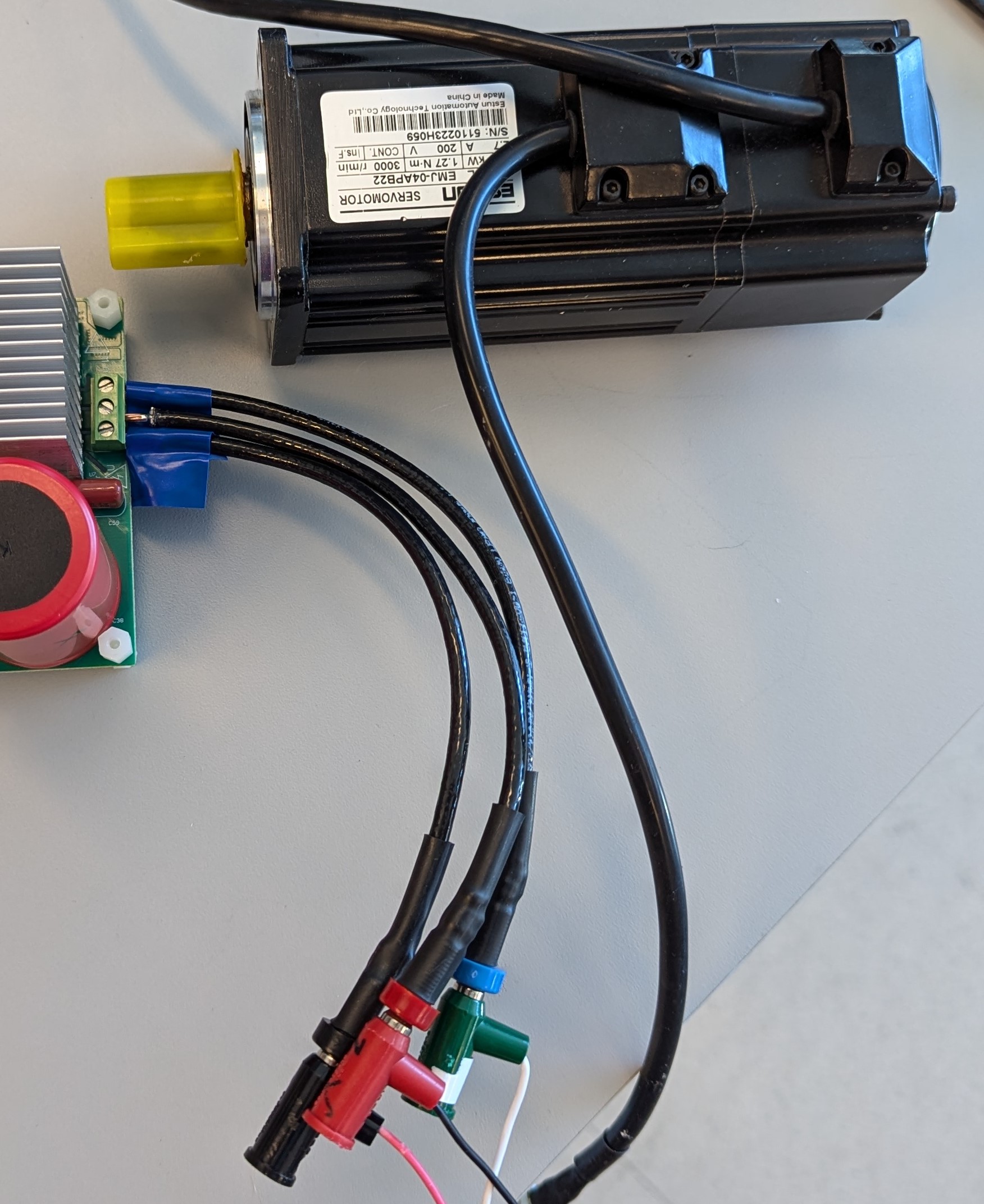
- Connect measurement equipment, such as multimeter, oscilloscope probes, and so forth, to probe or analyze various signals and parameters. Available test points can be viewed in the board schematic (TPx).
- Power on the board with isolated AC or DC power supply to the J5 ACL, ACN, and Earth connector.
- The maximum output of the AC power supply is 265-VAC, 50/60Hz.
- The maximum output of the DC power supply is 380-VDC.
The following options are also available.
- Daughterboard connector J4 pins 4 through 7 are available as SPI signals, should the user require external SPI. When doing so, the XDS110ISO-EVM on-board DAC is not available. This connection can be used by either:
- Connecting directly to the SPI signals on daughterboard connector J4. This connection is NOT isolated, and an external isolator must be used.
- Connecting to isolated UART interface J14, which may not be available on certain board revisions.
- If using this connection, depopulate daughterboard resistor R8 to ensure that the XDS110ISO-EVM on-board DAC does not interfere with the SPI peripheral-to-controller signals.
- The default board state utilizes three-phase current sensing. Should single-phase be required, refer to Section 2.1.4.2.